Leading North America construction services firm expands involvement in the mass timber market
Graham Construction, a Canadian-based construction solutions provider, is deepening its experience in the mass timber construction market—eager to meet evolving industry trends and pave a path toward a more sustainable future.
Graham is an employee-owned general contracting company operating across North America in all sectors of construction, with revenues of approximately $5 billion annually. The firm brings over nine decades of expertise to building projects of all kinds, demonstrating a legacy of consistent success and evolution in the changing world. Now, its team is working to expand its expertise in emerging green construction technologies like mass timber.
In an effort to expand its company-wide knowledge on the practice, Graham has brought on board Sustainability Manager Buildings Radek Pilarski, who has years of experience working on sustainable building practices across Europe and North America. Pilarski is now part of Graham’s Shared Services Buildings division, supporting the firm’s work with specialist knowledge across all phases of project delivery.
“I’m looking into green buildings for Graham. I bring a lot of hands-on experience from other parts of the world where this topic has been explored in great depth, but I’m also researching the latest local and international developments and helping Graham to connect the dots. The point is to understand what the new technologies, codes and standards mean for us and make us better at working with our client teams and trade partners,” Pilarski says. “The growing green buildings focus within the industry is opening new markets, like deep energy retrofits or mass timber projects. But it also means that we have to learn and evolve.”
By applying its scale, capacity, operational systems and construction know-how to this emerging construction segment, Graham seeks to support North America’s adoption of mass timber and be a solid and reliable partner for any clients seeking to build mass timber projects.
Building the portfolio
Mass timber construction has been used for some time across Europe, with international consultants, producers and installers developing the approaches and systems necessary to make mass timber cost-effective, high-performing and safe for buildings of all kinds. The technology has also existed in North America for some time, but it’s only relatively recently that it has become a serious focus of attention. The building approach has increasingly appealed to a variety of clients, both public and private, that see the methodology’s benefits.
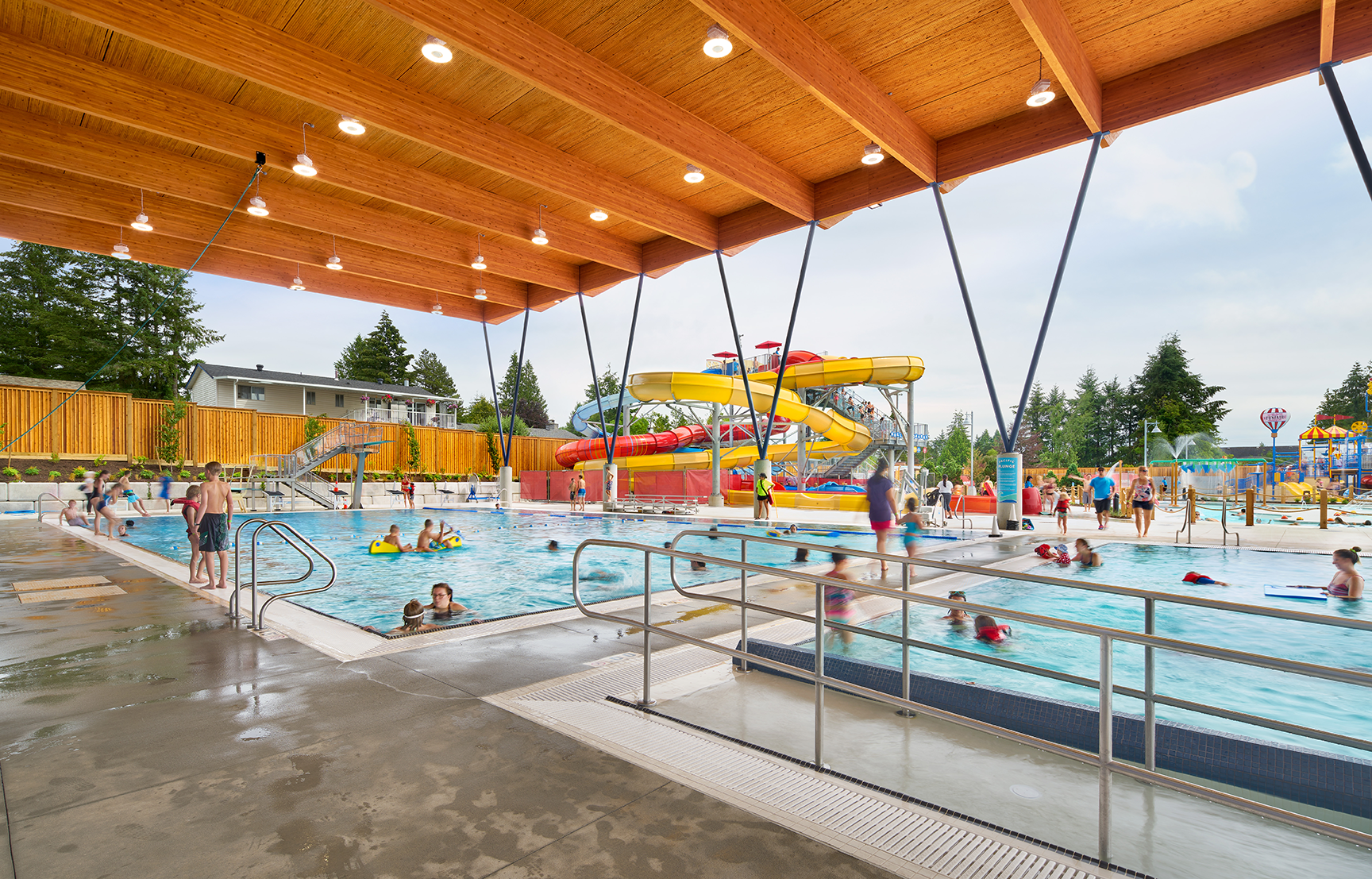
Aldergrove Credit Union Community Centre (Aldergrove, BC)
Primarily, mass timber is a sustainable approach that significantly decreases the embodied carbon of a structure compared to other materials like concrete and steel. Mass timber is a naturally growing material that doesn’t produce large amounts of carbon dioxide to be turned into a construction material. It’s also biodegradable and recyclable. All of these things appeal greatly to organizations looking to fulfill sustainability targets and minimize the carbon footprint of the buildings they develop. During production and installation, mass timber also reduces traffic volume, is much lighter than conventional materials, requires fewer workers on-site and can be built faster—resulting in time and cost savings on many projects. Although the benefits are plentiful, mass timber is still an evolving approach. Mass timber has typically been used for building components like feature roofs or building canopies made of glulam. Advancements in production and installation methodology have helped mass timber materials span larger distances, bear heavier loads and be more resilient to fire, allowing for full-building mass timber construction. As organizations learn more about mass timber’s benefits—and municipalities adjust building codes to allow greater applications of the material—more and more project leaders are inquiring about full-facility mass timber construction. It’s this market that Graham is pursuing.
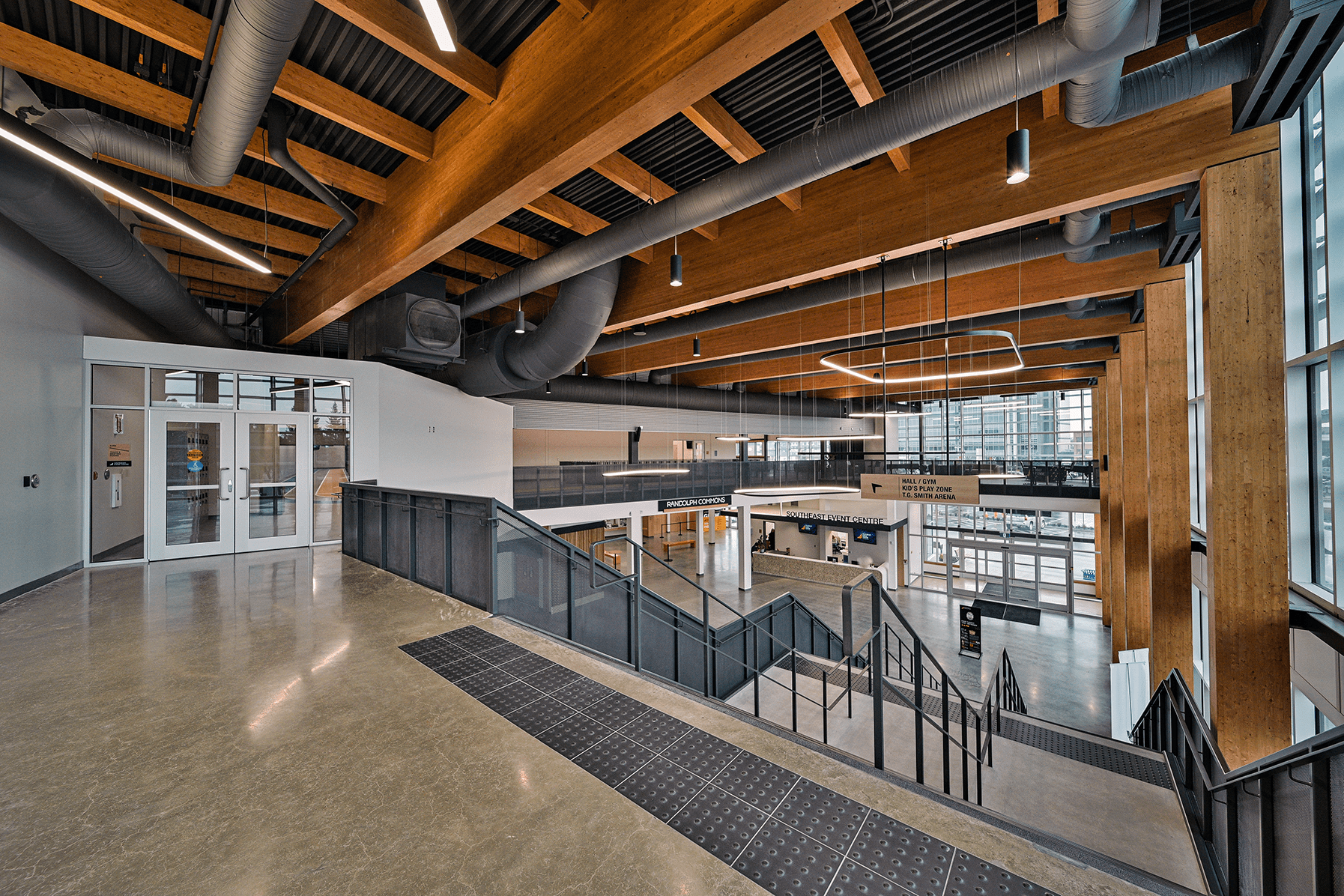
Southeast Event Centre (Steinbach, MB)
Already, the company has several whole-building mass timber projects under its belt, and it’s bidding for more that will emerge in the coming years. One of these facilities will open later in 2025: The Lawson Centre for Sustainability at Trinity College in Toronto. This 165,000 square-foot academic and residential facility will host new student housing and academic and common spaces, including a dining venue and rooftop urban farm. The four-story mass timber structure uses concrete foundations, cores and select slabs for structural bracing but is primarily built with CLT floor slabs, exposed CLT wall and façade panels and glulam beams and columns.
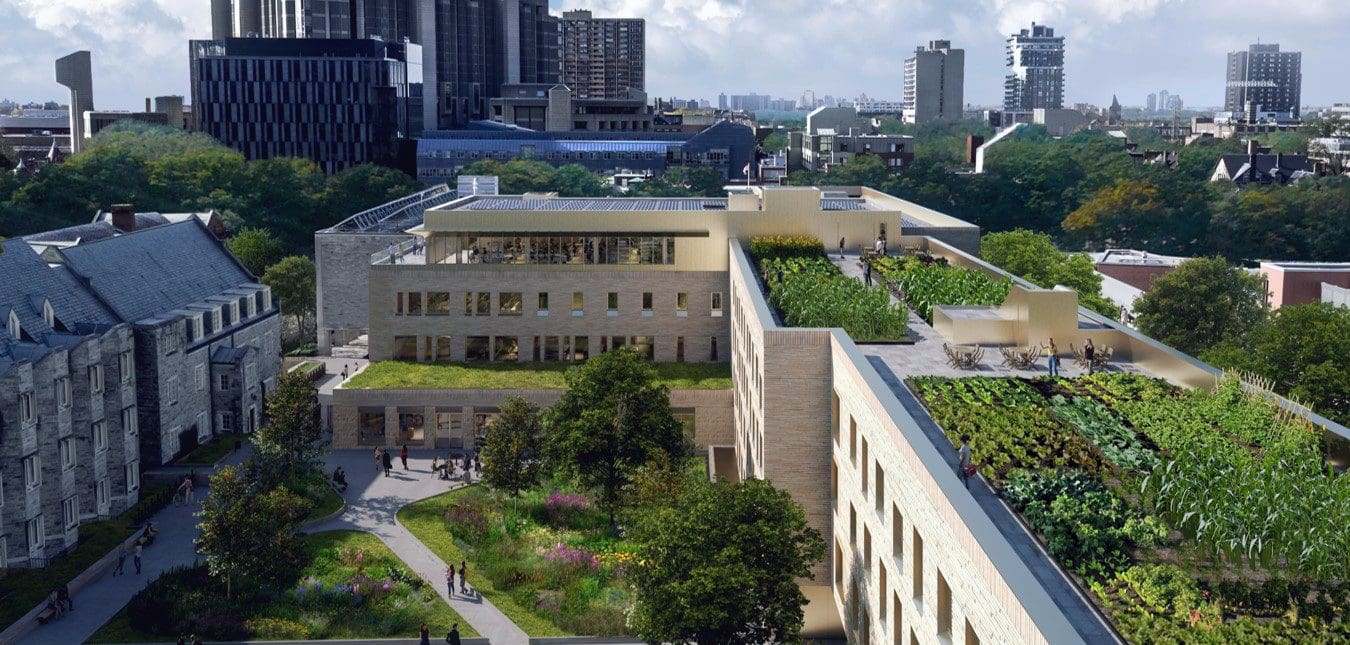
The Lawson Centre for Sustainability, Trinity College (Toronto, ON)
Another project, the new Cameron Community Centre and Library, is just getting started, with completion expected in late 2027. This will be a 213,000 square-foot replacement facility for the City of Burnaby, encompassing a library, an aquatic center, gymnasiums, fitness facilities, childcare areas and outdoor entertainment spaces. The two-story structure will be built with a hybrid of composite steel and mass timber, including CLT roof and floor slabs, glulam beams and columns and extended CLT canopies.
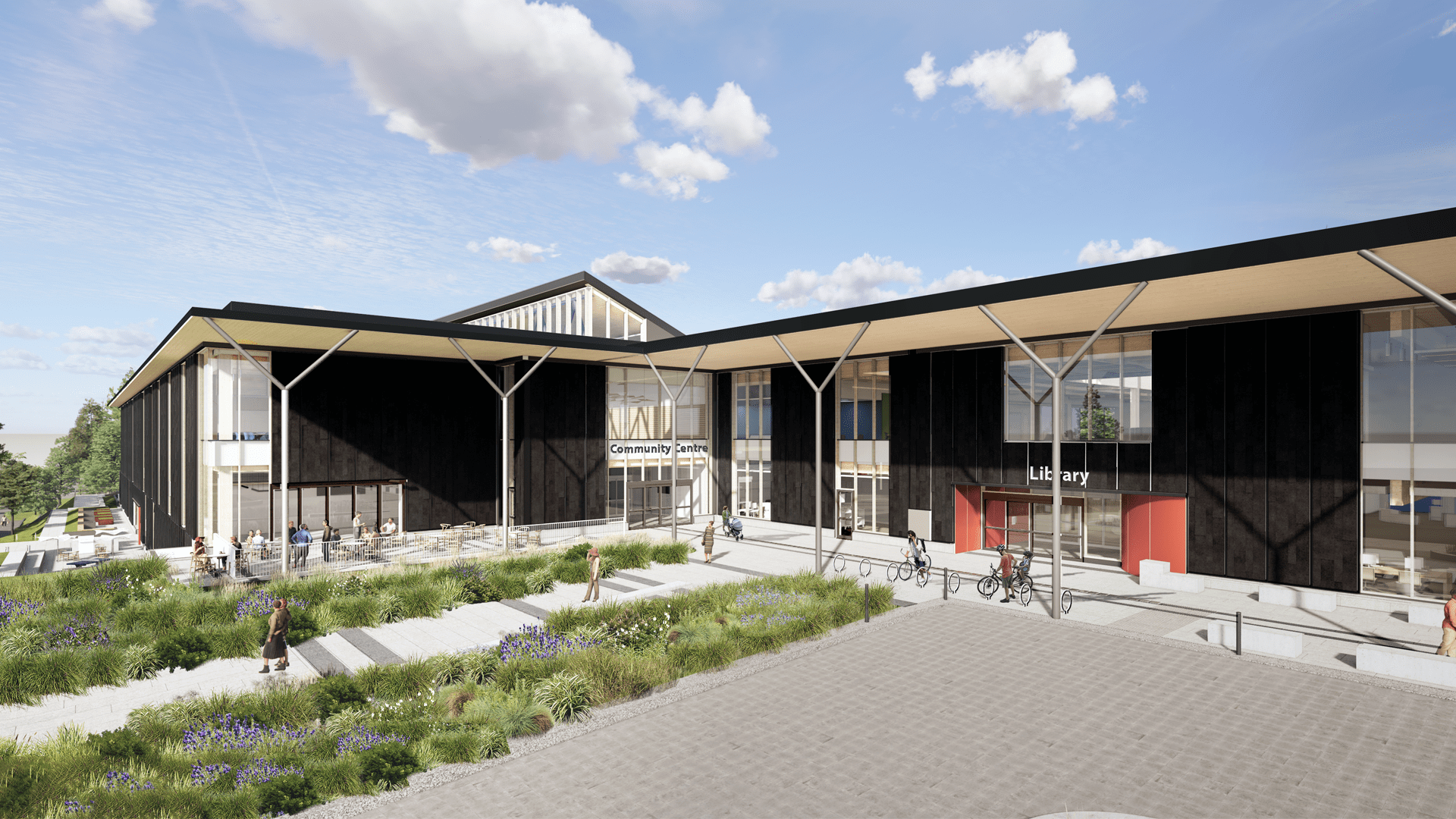
Cameron Community Centre and Library (Burnaby, BC)
As Graham’s project teams execute these mass timber projects, they continue to develop best practices that will inform their future endeavors and contribute to the evolution of the technology. Many of their traditional building skills transfer over—namely, supply chain experience and influence, partnerships with skilled trades, significant operational capacity and large-scale project coordination systems. However, the firm’s work in the early project stages is becoming more and more critical.
“The crux of the matter is that mass timber in many ways reshapes the approach to projects for any general contractor. With mass timber, preconstruction becomes the heavy-lifting phase of the project,” says Pilarski. “It requires a step change in your mindset to construction, because it means we and our trade partners have to be involved early and often plan our approach differently to what we are used to. There is a large amount of knowledge among our trade partners about how mass timber is produced and put together. We can tap into this to avoid making unnecessary errors. On the other hand, we as the general contractor have to truly understand the design and make sure that everything is perfectly coordinated so that when we actually get to site, we know that we can be faster than concrete.”
Pilarski stresses that mass timber construction can hold risks if it’s not produced, executed or installed by knowledgeable partners. It’s essential to get the team working together early, with all their collective strengths, and create a plan for fast buildout to minimize moisture and sun exposure, improper connections and other points of failure. For example, Graham’s work in BIM/VDC and clash detection in the preconstruction stage has helped minimize problems on the construction site, allowing for seamless installation on projects like Trinity College.
“You need VDC modeling and clash detection before you install—actually, before you produce the components—to make sure that penetration with pipes, connections with walls, with columns and steel connections, that it all fits. It is not optional,” Pilarski says. “You have to do it, because if you don’t, then your Lego blocks don’t fit together when you hit the site.”
Expanding education
Mass timber construction is not a perfected methodology, and partners at every step of the process—consultants, designers, producers and installers—are still learning and adapting their methods to minimize risk. It’s essential to build the right team with the right knowledge, as the industry is still evolving. Graham is devoted to becoming that right partner for its clients.
To do this, Graham is expanding its internal mass timber know-how, forging critical industry partnerships and developing better systems. Its recent mergers with companies like Milender White and XL Construction—both of which have mass timber construction experience in the U.S.—provide Graham with new perspectives and allow the firm to execute mass timber projects on a broader scale. The firm is also building stronger internal processes for estimating and bidding, quality assurance and CO2 measurements to execute projects more effectively.
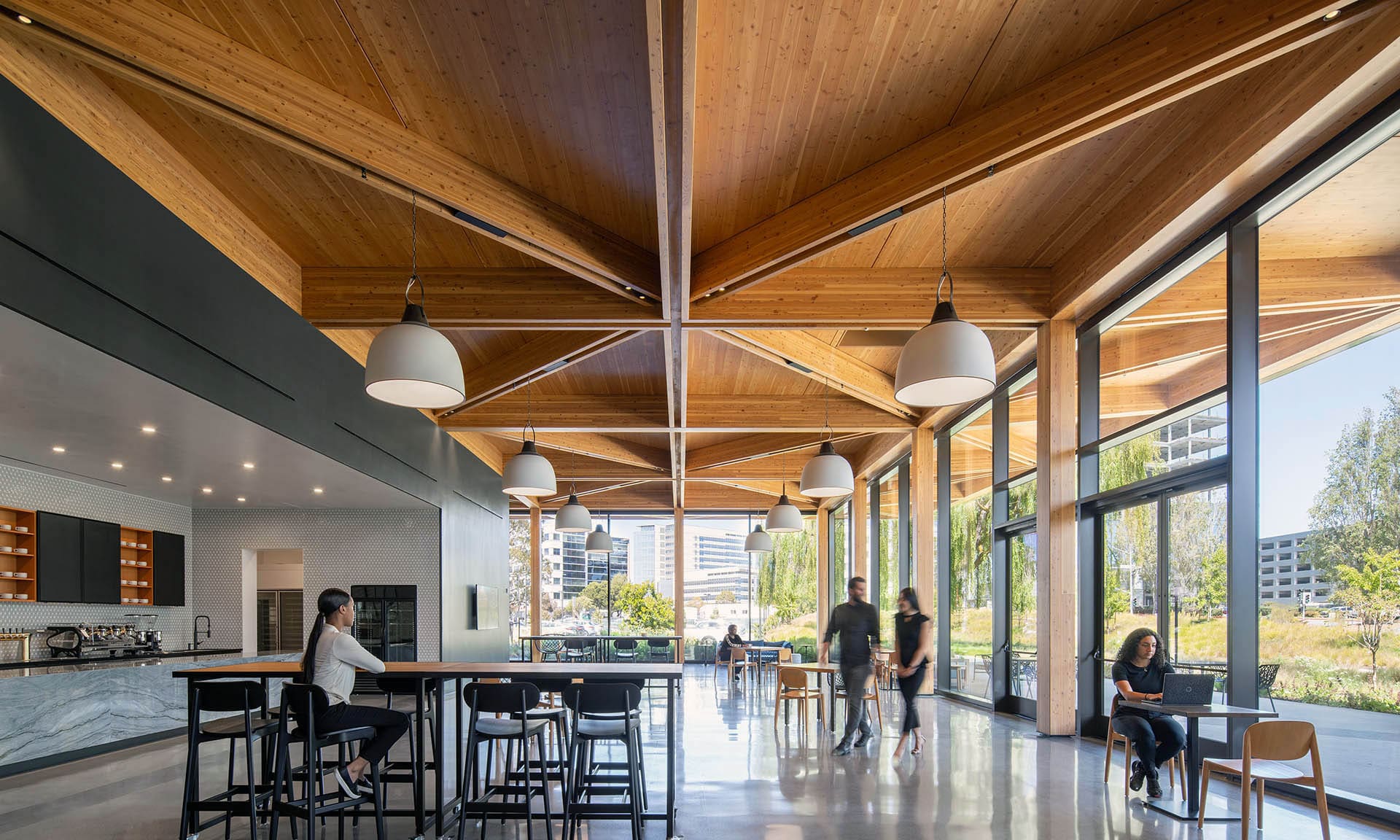
The Lighthouse (San Francisco, CA)
Graham’s focus on green building initiatives like mass timber supports its overall sustainability strategy and goals. But by keeping an open mind and remaining dedicated to adaptation, Graham is also driving a positive change that will benefit the industry as a whole.
“We have systems and processes in place to ensure that this knowledge is not only learned but also shared across the whole company and made available to others,” Pilarski says. “This is the advantage of being a tier 1 company with well-developed systems for continuous improvement. We need to keep our minds open, follow the cutting edge of the technology and learn from it. But we are also able to turn it into standards that can be introduced to the rest of the industry.”
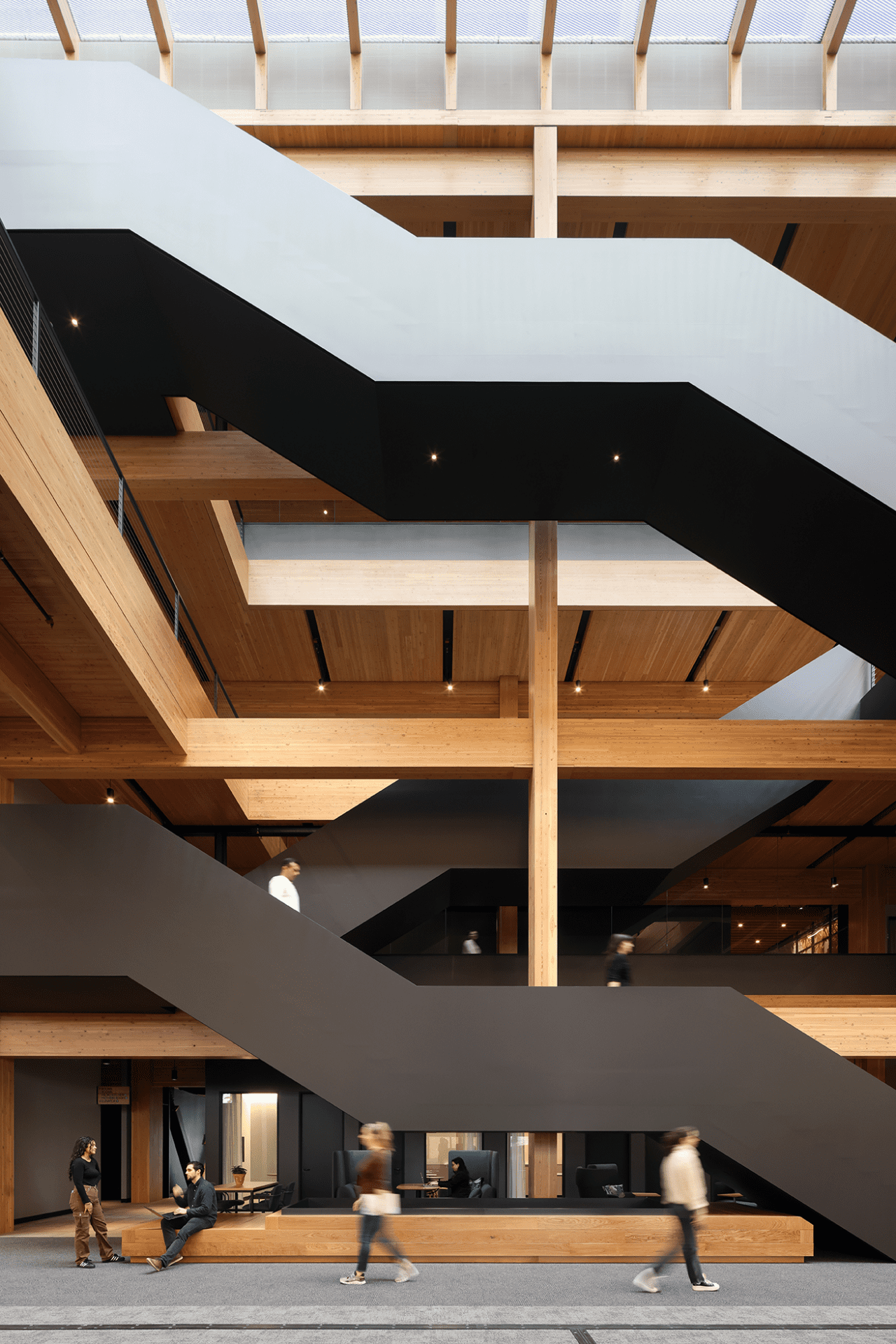
Google 1265 Borregas (Sunnyvale CA) Photo by: Mark Wickens
Article originally published in DDC Journal, Summer 2025 ed. (pg. 114) under title “Embracing Sustainable Construction“